The Challenge
In 2014, Saulsbury had over 50,000 assets in the hands of approximately 3,000 employees spread across multiple job sites nationwide. Although the company used an ERP platform, its tool and equipment inventory control relied on pen-and-paper clipboards. These manual processes led to inaccurate information and unacceptable amounts of lost time and assets, all of which Saulsbury knew were negatively impacting project performance and company profits.
One pressing example of this was the amount of time field workers wasted each day waiting to pick up tools: there was a 30-60 minute wait outside the tool room each day—a time-consuming and costly routine. Over the course of a year, this was stealing three to five weeks of productivity per worker, just waiting for the tools they needed. The process relied heavily on handwritten notes and was difficult to track, making accountability for tangible assets very difficult to enforce on warehouse staff, field management, and foremen. Meanwhile, the management of trailers, trucks, and tool vans fell under the fleet team’s purview, further complicating asset visibility.
To address this problem, Saulsbury wanted more than to know where its tools and equipment were and how many they had. The company also wanted to create accountability and manage those assets proactively to solve real business problems.
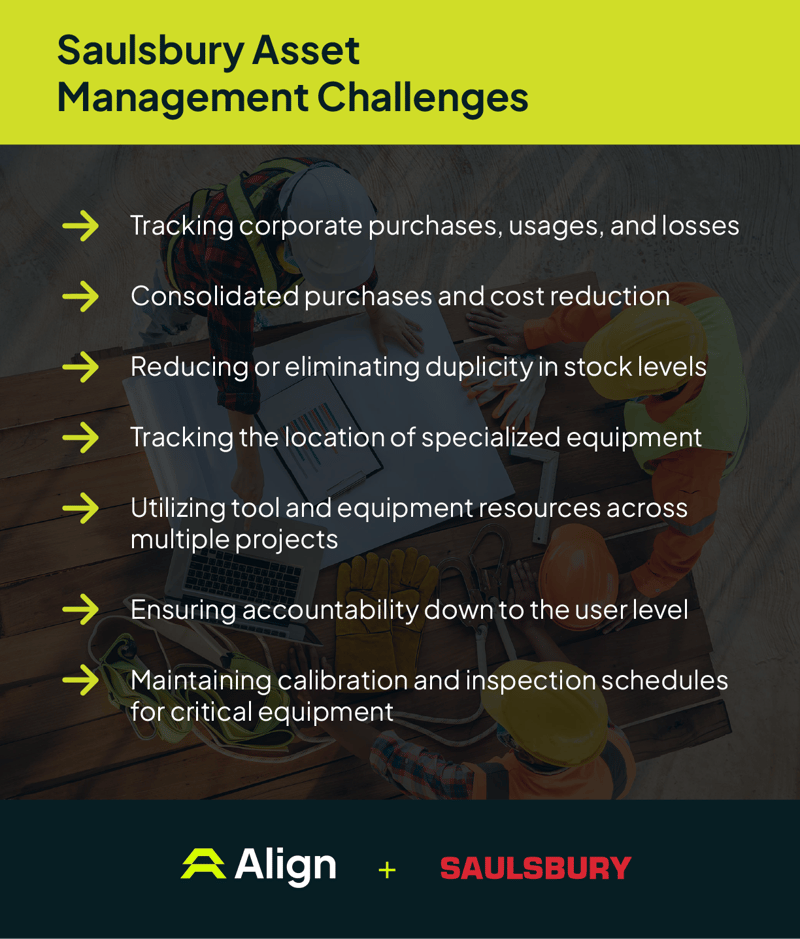
Saulsbury needed a scalable solution for its construction enterprise that would provide the accurate location of assets, create accountability among the field team, support warehouse logistics like pick tickets and equipment service, and provide the back office with financial data to bill jobs and inform strategic business decisions.